Filing Requirements for Onshore Drilling Operations Involving Hydraulic Fracturing
Filing Requirements for Onshore Drilling Operations Involving Hydraulic Fracturing [PDF 693 KB]
Copyright/Permission to Reproduce
September 2013
Table of Contents
- 1.0 Introduction
- 2.0 Environmental Assessment
- 3.0 Operations Authorization
- 3.1 Proof of Financial Responsibility
- 3.2 Declaration by Applicant or by Owner
- 3.3 Management System
- 3.4 Management System Implementation
- 3.5 Safety Culture
- 3.6 Human Factors
- 3.7 Lessons Learned
- 3.8 Safety Plan
- 3.9 Risk Assessment
- 3.10 Environmental Protection Plan
- 3.11 Waste Management
- 3.12 Spill Contingency Plan
- 4.0 Well Approval
- 5.0 All-Season Well Pads
- 6. 0 Inter-Well Distances on Multi-Well Pads
1.0 Introduction
The National Energy Board (NEB or Board) is an independent federal agency established in 1959 by the Parliament of Canada. The NEB has regulatory responsibilities for oil and gas exploration and production activities, including the drilling, completion, hydraulic fracturing and formation flow testing of, and production from onshore unconventional reservoirs under the Canada Oil and Gas Operations Act (COGOA)Footnote 1 and its regulations. The purpose of COGOA, among other things, is to promote safety, protection of the environment and the conservation of oil and gas resources.
While the NEB may issue authorizations pursuant to paragraph 5(1)(b) of the COGOA, the NEB does not administer the following processes: land tenure and rights issuance (exploration licences, significant discovery licences and production licences), royalty management and benefits plans. Applicants should contact Aboriginal Affairs and Northern Development Canada or Natural Resources Canada for further information on these matters.
1.1 The Purpose of the Filing Requirements
The Filing Requirements for Onshore Drilling Operations Involving Hydraulic Fracturing (Filing Requirements) should be used in all cases where a proposed work or activity requiring an Operations Authorization (OA) involves hydraulic fracturing.
These Filing Requirements outline the information the Board will need to assess future applications for drilling that involve hydraulic fracturing.Footnote 2 The Filing Requirements apply to hydraulic fracturing operations in the Northwest Territories and Nunavut.
These Filing Requirements focus on the unique elements of hydraulic fracturing. The Board expects each applicant to submit the information described in the Filing Requirements with its application for an OA. Additional information may need to be submitted with each subsequent application for an approval, such as a Well Approval or Formation Flow Test Approval.
The information set out in the Filing Requirements does not prevent the Board from requesting any additional information it may find relevant, or from waiving certain Filing Requirements if they are not relevant to the applied-for work or activities. The applicant is responsible for complying with all applicable statutory and regulatory requirements. Accordingly, the Filing Requirements should be read in association with the COGOA and its regulationsFootnote 3, particularly the Canada Oil and Gas Drilling and Production Regulations (COGDPR) and any guidelines issued by the NEB regarding these regulations.
The Filing Requirements are not static and will be updated periodically. The Board is committed to continually improving its regulatory process so that its decisions on applications for all authorized works or activities regulated under COGOA promote safety, protection of the environment and conservation of oil and gas resources.
2.0 Environmental Assessment
As part of its environmental protection responsibilities, the NEB makes sure that an environmental assessment (EA) is conducted for proposed activities in the Northwest Territories and Nunavut. The NEB conducts its own EA prior to issuing an OA as well as coordinating EAs with the northern boards or committees established by the Mackenzie Valley Resource Management Act (MVRMA)Footnote 4, the Inuvialuit Final Agreement (IFA) and the Nunavut Land Claims Agreement (NLCA)Footnote 5. An EA must be completed before a COGOA authorization can be issued. Environmental Assessment
The NEB relies on a proponent’s project description to coordinate EAs with northern boards and agencies. Accordingly, proponents are encouraged to provide a project description to the NEB as early as possible. See Section 2.2 for further details.
2.1 Proposed Project Location
Proposed development projects that occur in the Mackenzie Valley require a preliminary environmental screening, EA or review under Part 5 of the MVRMA. A preliminary screening is conducted by a Land and Water Board (LWB). Projects may also be referred to the Mackenzie Valley Environmental Impact Review Board (MVEIRB) which carries out EAs and public reviews.
Pursuant to the MVRMA, the NEB does not issue an OA until the LWB or MVEIRB has issued its decision. The NEB considers the recommendations made by the LWB or MVEIRB before it decides, on the basis of environmental impact considerations, whether or not the proposed work or activities should proceed and, if so, on what terms and conditions, including mitigative measures.
Figure 1: Mackenzie Valley
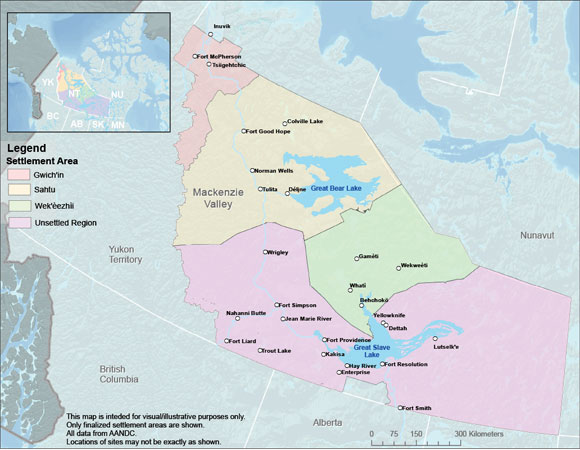
This map is inteded for visual/illustrative purposes only. Only finalized settlement areas are shown. All data from AANDC.Locations of sites may not be exactly as shown.
Proposed work and activities that occur in the Inuvialuit Settlement Region require an environmental screening or review under the Inuvialuit Final Agreement. An environmental screening is conducted by the Environmental Impact Screening Committee (EISC). Projects may be referred to the Environmental Impact Review Board (EIRB) which carries out environmental impact assessments and public reviews. Proponents should provide the same information to the NEB and EISC or EIRB so that conclusions are based on the review of consistent information.
Typically, during the EISC or EIRB processes there is extensive consultation that ensures local perspectives and issues are identified. The IFA addresses the prevention of loss or damage to wildlife and habitat and subsequent compensation if there is loss in terms of harvesting opportunities.
The IFA requires the NEB to wait for an EISC or EIRB decision before issuing any regulatory authorization. The NEB considers the recommendations before it decides, on the basis of environmental impact considerations, whether or not the work and activities should proceed and, if so, on what terms and conditions, including mitigative measures.
Figure 2: Inuvialuit Settlement Region
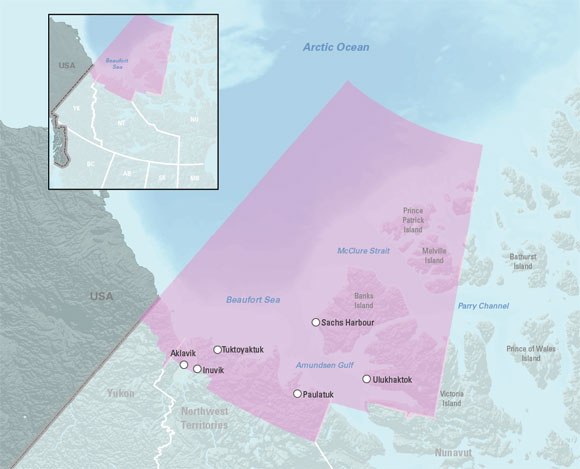
The Nunavut Impact Review Board (NIRB) screens proposed projects in the Nunavut Settlement Area (NSA) under the Nunavut Land Claims Agreement to determine whether or not an environmental impact review is required. The NEB will keep the NIRB updated on the NEB EA process and, although the NIRB may not be a party to the EA, the NIRB is able to provide comments during the EA process.
Typically, for projects located completely outside of the NSA, the proponent will provide project information to the NIRB to determine if potential trans-boundary impacts would trigger an assessment under the NIRB.
Figure 3: Nunavut Settlement Area
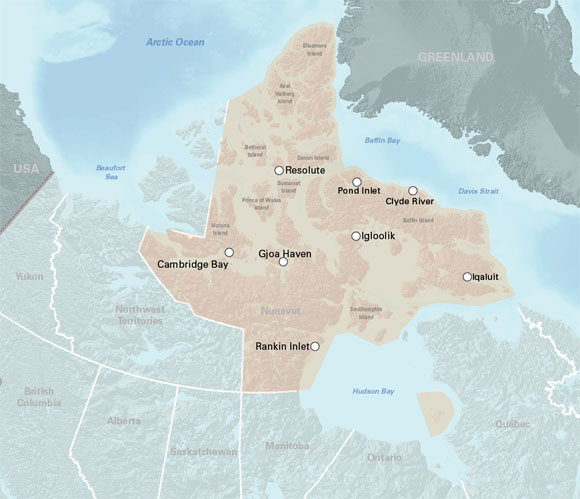
2.2 Project Description Content for the Purpose of EA
The project description is to include detailed information on: the project development; potential impacts to the environment, including potential impacts from accidents and malfunctions; consultation with Aboriginal groups and the public; socio-economic impacts arising from environmental impacts; and mitigation measures to protect the environment.
The following filing requirements describe the information to be included in a project description. Information about details to be provided in a project description may also be found under a number of sources, depending on where the project is located, including:
- Mackenzie Valley Review Board, Environmental Impact Assessment Guidelines;
- EISC, Environmental Impact Screening Guidelines;
- EISC, Environmental Impact Screening Guidelines, “provide guidance and direction to parties participating in the environmental screening of proposed developments” in the ISR;
- EISC, Environmental Impact Screening Guidelines, Appendix F: Example Project Description Submission Content Guide;
- EIRB, Environmental Impact Review Guidelines; and
- NIRB, Guide 3 - Filing Project Proposals and the Screening Process, Guide 5 - The NIRB Review Process, and Guide 7 - Preparation of Environmental Impact Statements.
Proponents should provide the same information to the NEB and northern boards and agencies so that conclusions are based on evaluation of consistent information.
2.2.1 Consultation
Context
The applicant is required to consult with persons or groups who may be affected by the proposed project. The extent of consultation required for any given application will depend on the nature of the project and its scope. The project description should provide the results of the consultation conducted and offer sufficient details to justify the extent of that consultation. It should also offer a description of what other consultation activities will be carried out.
Goal
The project description provides evidence to outline the policies and principles by which an applicant will ensure that it adequately consults with, and respects the rights of, those potentially affected. The project description also describes the project’s consultation program and explains why its design and implementation are appropriate for the nature of the project and its scope.
Filing Requirements
- Provide an overview of the consultation approach, including:
- the policy or vision with respect to consultation;
- the principles and goals established for the project’s consultation program;
- a copy of the consultation protocol, if established, along with any documented policies and principles for collecting traditional knowledge or traditional land use information, if applicable;
- identifying any government authorities (Aboriginal, local, territorial, and federal) which were included in the consultation process;
- demonstrating that all groups or persons potentially affected by the project have been made aware of the project and are aware of approximately when the project application to the Board will be filed; and
- identifying the groups or persons potentially affected by the project who have been consulted, along with a summary of their concerns and comments.
- Provide a summary of the response made regarding each of the concerns or comments identified above, including:
- the measures taken, or that will be taken, to address those concerns or an explanation of why no further action is required to address the concerns or comments;
- how outstanding concerns will be addressed; and
- how information from persons or groups, including local and traditional knowledge, has influenced the design or operation of the project.
2.2.2 Socio-Economic Impacts
Goal
The project description provides sufficient detail to demonstrate an understanding of how the project will affect the social, cultural and economic status of residents and communities in the region or area where the project is located and what measures will be implemented to protect their well-being.
Filing Requirements
- Provide information in the project description regarding the social, cultural and economic status of regional area residents and communities.
- Describe what measures will be implemented for the protection of the social, cultural and economic status of regional area residents and communities.
3.0 Operations Authorization
The NEB may issue an authorization for each work or activity proposed to be carried out. An authorization may be subject to terms and conditions that the NEB determines. The Operations Authorization and the Well Approvals are the primary regulatory permissions necessary to conduct a drilling program. Other non-NEB permits, licences or authorizations may also be required.
An Operating Licence is a prerequisite to carry out any oil and gas work or activity. Any individual or corporation may apply to the NEB for an Operating Licence. For additional information regarding an Operating Licence, refer to the Canada Oil and Gas Operations Regulations.
3.1 Proof of Financial Responsibility
Applicants should refer to the Draft Financial Viability and Financial Responsibility GuidelinesFootnote 6 for information.
3.2 Declaration by Applicant or by Owner
Goal
The application provides a declaration by the applicant or by the owner in accordance with section 5.11 of COGOA confirming that equipment and installations are fit for their intended purposes throughout the proposed activities.
Filing Requirements
- Provide a declaration executed by the most senior accountable officer of the applicant or owner that, at commencement and throughout execution of the activities, the equipment and installations that are to be used in the work or activities are fit for the locations and purposes for which they are to be used, the operating procedures relating to them are appropriate for those uses, and the personnel who are to be employed in connection with them are qualified and competent for their employment.
- Describe the processes used to monitor compliance with the declaration by applicant or by owner. Describe the actions taken should the applicant find a violation of any condition upon which its declaration was made, which should include taking immediate corrective action or ceasing the activity until such time as the validity of the declaration can be re-established.
3.3 Management System
Goal
The application describes the management system with enough detail to demonstrate:
- the integration of operations and technical systems with financial and human resource management for the purposes of achieving safety, security, environmental protection, and conservation of resources;
- how the system ensures compliance with the COGOA and its regulations, and any authorizations and approvals issued by the Board;
- that it applies to plans, programs, manuals, and systems required under the COGOA and its regulations;
- that it corresponds to the size, nature, and complexity of activities authorized under the COGOA and its regulations, and the associated hazards and risks; and
- that it provides a strong foundation for a pervasive culture of safety, forcefully affirmed by the organization’s leadership, rigorously documented in writing, known to all employees and contractors involved in safety and environmental protection, and consistently implemented in the field.
Filing Requirements
- Identify the name and position of the person accountable for the establishment, implementation and maintenance of the management system. Provide evidence of their acceptance of these responsibilities.
- Identify and describe the policies upon which the system is based, including goals and objectives respecting management and improvement of process and occupational safety, security, environmental protection and conservation of resources.
- Describe and provide supporting evidence of the applicant’s organizational structure to meet the requirements of the management system, which clearly identifies and communicates roles, responsibilities and authorities at all levels of the applicant. Demonstrate and substantiate that resourcing is adequate based on the size, nature and complexity of organizational activities.
- Identify positions critical to safety within the organization and provide a job description for each.
- Demonstrate that the management system has systematic, explicit, comprehensive, proactive, and documented processes for:
- the development of annual objectives and targets related to safety, security, environmental protection, and conservation of resources, and a means to measure these objectives and targets;
- the identification and analysis of potential hazards, including the maintenance of an inventory of hazards;
- the evaluation and management of risks associated with all hazards, including the risks related to normal and abnormal operating conditions, and the development, implementation, and communication of preventative, protective, and mitigative measures for identified hazards and risks;
- incorporating contractors, subcontractors, and any service providers;
- ensuring and maintaining the integrity of all facilities and equipment necessary to ensure safety, security, environmental protection, and conservation of resources;
- the identification and monitoring of applicable acts, regulations, approvals, and orders as they relate to the applicant’s obligations with respect to safety, security, protection of the environment, and conservation of resources, and the maintenance of a table of concordance to monitor compliance and identify and resolve any non-compliance;
- the identification and management of any changes in the applicant’s activities that could affect safety, security, environmental protection, or conservation of resources, including changes related to new hazards, risks, designs, specifications, standards, procedures, organizational changes, and legal requirements;
- the establishment of competency requirements and effective training programs so that employees, contractors, subcontractors, service providers and any other persons working with or on behalf of the applicant are trained, competent, and appropriately supervised to perform their duties;
- i. internal and external communications that support safety, security, environmental protection, conservation of resources, and the effective implementation and operation of the applicant’s management system;
- ensuring that the records supporting and demonstrating the implementation of the management system and related requirements are developed, retained, accessible, and maintained;
- the identification of documentation requirements for the development, review, revision, and control of documents, with approval by the appropriate authority for effective implementation of the management system;
- the coordination and management of activities undertaken by employees, contractors, subcontractors, service providers and any other persons who could be working with or on behalf of the applicant or operator;
- the internal reporting of hazards, near misses, and incidents and the maintenance of measures for taking corrective actions to prevent their recurrence, including a data system to monitor and analyze trends;
- preparation and response for safety, security, environmental incidents, and emergency situations;
- monitoring, measuring, and recording safety, security, environmental management, and resource conservation performance to evaluate the implementation and effectiveness of the management system;
- a quality assurance program to improve the activities authorized under the COGOA and the COGDPR; and
- a process for conducting audits and reviews of the management system and taking corrective and preventative actions if a non-compliance is identified.
3.4 Management System Implementation
Goal
The application describes the management system oversight program with enough detail to demonstrate that:
- it has been fully implemented across the organization and is functional for the purposes of achieving safety, security, environmental protection, and conservation of resources;
- all hazards that pose a threat to the safety and integrity of drilling and fracturing operations, including those related to human factors, have been identified and mitigated; and
- it is subject to an internal quality assurance process for continual improvement.
Filing Requirements
- Describe and provide supporting evidence of the most recent internal and external management system audits, including the corrective and preventative action plans generated as a result of any related findings.
- Describe all hazards identified in association with this project, including the methods used to eliminate or mitigate the related risks.
3.5 Safety Culture
Goal
The application describes the management system with enough detail to demonstrate organizational commitment and support for the development and maintenance of a positive safety culture.
Filing Requirements
- Describe and provide supporting evidence of the commitments, policies, practices, and programs that support continual improvement of the organization’s safety culture, including that of contractors, subcontractors, service providers and any other persons who could be working with or on behalf of the applicant.
- Describe and provide evidence of leadership commitment and acceptance of accountability for safety performance by the most senior executive of the organization.
- Describe how the organization measures safety culture and provide the results from the most recent assessments, including employee perception survey results.
- Provide a copy of the action plan designed to respond to the safety culture assessment and to support the development and maintenance of a positive safety culture.
- Describe how workers will be actively engaged in the process of safety management throughout the life cycle of the project.
- Describe and provide evidence of the organization’s policy and procedures for safety “stand downs”, including the conditions and activities during which this practice is deemed mandatory.
- Describe how the organization encourages workers to actively report safety threats, hazards, near-misses, and incidents without fear of recrimination.
- Provide evidence of the applicant’s stop work authority policy and its implementation. Describe how this authority is exercised by workers. Describe how the policy, procedure, and related responsibilities are communicated to all contractors, subcontractors, service providers and any other persons who could be working with or on behalf of the applicant.
- Describe how the organization would implement, maintain, assess, and improve safety culture for a project when activities are of short duration or are discontinuous.
- Describe how a safety culture is maintained during periods when there is no activity or when there is a change to the crew.
3.6 Human Factors
Goal
The application describes the management system with enough detail to demonstrate that:
- human performance has been taken into consideration during project planning and risk assessments; and
- the human performance challenges associated with drilling and hydraulic fracturing activities have been addressed.
Filing Requirements
- Describe how human factors are identified and addressed during the project planning phase in order to effectively manage the potential for human error during drilling and hydraulic fracturing operations.
- Provide a list of all human factors assessed and the proposed controls, including those which are unique to the operational environment.
3.7 Lessons Learned
Goal
The application describes the management system with enough detail to demonstrate that lessons learned from internal and external incidents and near-misses are incorporated into policies, processes, and procedures, and to ensure continual improvement.
Filing Requirements
- Describe the process by which lessons from incidents and near-misses in the organization and across the industry are and will be incorporated into the organization’s management system and related programs.
- Describe how these lessons will be communicated to all workers to ensure they are aware of potential threats, hazards, and remedies.
3.8 Safety Plan
Goal
The applicant must include a Safety Plan in all applications for an authorization. See section 8 of the COGDPR as well as the Safety Plan Guidelines,Footnote 7 for further information on the contents of a Safety Plan. The Safety Plan should provide enough detail to demonstrate the procedures, practices, resources, sequence of key safety-related activities, and monitoring measures necessary to ensure the safety of the proposed work or activity.
Filing Requirements
- Provide evidence that the Safety Plan was developed in accordance with section 8 of the COGDPR and Safety Plan Guidelines.
- Provide a summary of and references to the management system that demonstrate how it will be applied to the proposed work or activity and how the duties set out in COGDPR with regard to safety will be fulfilled.
- Describe the organizational and command structure of the operator and contractors, subcontractors, service providers and any other persons who could be working with or on behalf of the applicant for each phase of the proposed work or activity.
- Provide up to date contact information and the position of the person accountable for the Safety Plan and of the person responsible for implementing it.
- Describe the compliance monitoring arrangement of the plan and performance measurement in relation to its objectives.
- Describe how the role of contractors, subcontractors, service providers and any other persons who could be working with or on behalf of the applicant will be incorporated into the Safety Plan.
- Describe how any changes to the Safety Plan will incorporated.
3.9 Risk Assessment
Goal
The application describes the applicant’s risk assessment and risk management processes with enough detail to demonstrate that the applicant has:
- effective processes in place to identify threats and hazards to safety and the environment, to identify and select effective mitigative measures, and to evaluate and manage the associated risks; and,
- taken, or will take, all reasonable precautions to ensure that safety and environmental protection risks have been addressed for the proposed work or activity, including taking into account the interaction of all components, including structures, facilities, equipment, operating procedures, and personnel.
Filing Requirements
- Provide a summary of the studies undertaken to identify threats and hazards and to evaluate risks to safety and the environment related to the proposed work or activity.
- Describe the processes and procedures used to identify and select all reasonable precautions pursuant to the requirements of section 19 of the COGDPR.
- Describe the risk assessment framework used to determine acceptable and tolerable levels of risk for the proposed work or activities.
- Identify the criteria used for deciding what is and what is not a reasonable precaution.
- Provide a description of the hazards that were identified and the results of the risk evaluation.
- Provide a summary of the measures to avoid, prevent, reduce and manage safety risks.
- Provide a list of all structures, facilities, equipment and systems critical to safety and environmental protection and a summary of the system in place for their inspection, testing and maintenance.
- Describe threats and hazards critical to safety identified for all stages or phases of the activities from design through to completion of operations including those related to:
a. facility and drilling unit integrity;
b. well integrity;
c. well control; and
d. hydraulic fracturing operations.
3.10 Environmental Protection Plan
Goal
Applications for authorizations include an Environmental Protection Plan (EPP). See section 9 of the COGDPR and the Environmental Protection Plan GuidelinesFootnote 8 for further information on the contents of an EPP. The EPP should provide enough detail to demonstrate:
- an understanding of how the work or activity will interact with the environment;
- that the EPP has the procedures, practices, resources, and monitoring necessary to manage hazards and to protect the environment from the impacts of the proposed work or activity, including potential impacts to groundwater;Footnote 9 and
- that the predicted environmental hazards and risks, including the preventive and mitigative measures in the EA are incorporated.
Filing Requirements
- Provide evidence that the EPP is developed in accordance with the applicable sections of the Environmental Protection Plan Guidelines.
- Demonstrate how the management system for the proposed work or activities will ensure that the duties set out in the COGDPR with regard to environmental protection will be fulfilled.
- Provide a summary of the studies undertaken to identify environmental hazards and to evaluate environmental risks relating to the proposed work or activity.
- Describe the species that would be particularly sensitive to emissions or spills of oil, hydraulic fracturing fluids, other fluids or emissions from well drilling, hydraulic fracturing or formation flow testing operations.
- Describe how any heritage resources, protected areas, species at risk and species at risk recovery strategies, such as for boreal caribou, will be addressed in the proposed work or activity.
- Identify the sources of fresh and saline water and their volumes required for drilling, hydraulic fracturing, completions, formation flow testing and/or production activities and provide an assessment of impacts to the environment and to area residents and communities.
- Provide a water quality assurance plan for how surface water and groundwater quality will be assessed, protected and monitored for impacts from planned and unauthorized discharges from drilling, hydraulic fracturing, flaring, and formation flow testing, well suspension and abandonment and production activities.
- Demonstrate how the impacts to the environment from air emissions during site access, handling and storage of produced fluids including formation and flowback fluids, flaring and formation flow testing operations would be minimized.
- Provide an air quality assurance plan that describes how air quality will be assessed, protected and monitored for impacts from planned discharges and fugitive or other unauthorized discharges from drilling, hydraulic fracturing, flaring, formation flow testing, storage of produced fluids including formation and flowback fluids, well suspension and abandonment and production activities.
- Identify the volumes of water that would be recycled, reused as fracture fluids, transported out of the region for approved disposal elsewhere, and/or disposed by deep well injection.
- Describe any knowledge gaps regarding the environmental setting of the work or activity (biological, physical, and geological) and how these gaps will be addressed.
- Describe how results of ongoing research or information gathering initiatives will be incorporated into the proposed work or activity.
- Describe the hazards to the environment that were identified and the results of the risk evaluation of those hazards.
- Describe the measures to anticipate, avoid, prevent, reduce, and manage environmental risks.
- Verify that the environmental protection measures, commitments and implementation plan will be provided to the appropriate employee, contractors, subcontractors, service providers and any other persons who could be working with or on behalf of the applicant, and that the measures will be reviewed with them prior to drilling, completion, hydraulic fracturing, flaring and formation flow testing operations, well suspension or abandonment operations and prior to production operations and annually thereafter.
- Describe all structures, facilities, equipment, and systems critical to environmental protection, and provide a summary of the system in place for their inspection, testing, and maintenance.
- Describe the organizational and command structure of the applicant and contractors, subcontractors, service providers and any other persons working with or on behalf of the applicant for each phase of the proposed work or activity.
- Provide the contact information and position of the person accountable for the EPP and the person responsible for implementing it.
- Describe the procedures for the selection, evaluation, and use of chemical substances, including process chemicals and drilling fluid ingredients.
- Indicate if the applicant is willing to publically disclose the chemicals used in the hydraulic fracture fluids.
- Describe the arrangements for monitoring compliance with the EPP and for measuring performance in relation to its objectives.
- Describe the processes and procedures to detect, report, investigate and correct the causes and causal factors of pollution (exceedances of discharge limits), and to prevent re-occurrences.
- Describe how the groundwater monitoring and sampling program will detect any contamination from oil and gas operations including hydraulic fracturing operations.
3.11 Waste Management
Context
“Waste material” is any garbage, refuse, sewage, waste well fluids, or any other useless material that is generated during drilling, completions, hydraulic fracturing, formation flow testing, well or production operations, including drill cuttings, used or surplus drilling and completion fluids, hydraulic fracture fluids, produced fluids including formation fluids and flowback fluids. Applicants are expected to take all reasonable measures to minimize the volumes of waste materials generated by their operations, and to minimize the quantity of substances of potential environmental concern contained within these waste materials. No substance should be discharged to the environment unless the Board has determined that the discharge is acceptable.
Goal
Applications must include a complete and adequate plan to manage discharged waste material.
Filing Requirements
- Provide evidence that the waste management plan was developed with reference to the applicable existing discharge standards, guidelines, objectives or best practices set out by government departments and agencies or industry.
- Describe the planned waste discharges, the limits of these discharges, and the equipment and procedures for treatment, handling, and disposal of waste material.
- Identify and reference any methods or protocols that were used to establish the discharge limits.
- Describe the equipment and procedures for the treatment, handling, and disposal of waste material.
- Describe any agreements or arrangements for disposal of waste material associated with drilling, completion, hydraulic fracturing and formation flow testing or production activities.
- Describe the arrangement for monitoring compliance with the waste management plan and for measuring performance in relation to its objectives.
- Provide details of incident reporting procedures in the event of exceedances of the discharge limits.
3.12 Spill Contingency Plan
Context
A spill contingency plan should provide emergency response procedures to mitigate environmental and safety impacts from unplanned or accidental discharges to the environment. Pollution, which includes spills, also refers to situations where discharges from authorized operations or activities exceed the authorized discharge limits.
Goal
Applications Contingency Plans for spill response will provide enough detail to demonstrate that effective systems, processes, procedures, and capabilities will be in place to:
- minimize the impacts to the natural environment from unauthorized or accidental discharges; and
- protect workers and the public.
Filing Requirements
- Describe the worst-case scenario for a loss of surface or subsurface containment of hydraulic fracturing fluids, formation fluids and flowback fluids.
- Describe the consequences of the worst-case scenario, including:
- the estimated flow rate;
- properties of the fluid released;
- the volume of fluid that could be released;
- the volume of fluid that would be recovered;
- the likely short-term impacts on the environment and communities;
- the residual long-term impacts on the environment and communities; and
- how long it would take to regain well control in worst-case operating conditions.
- Provide organization charts describing the emergency response command structure and responder positions, including the duties, responsibilities, and accountabilities for the various levels or tiers of emergency.
- Describe the process and procedures for containing and recovering, or eliminating and cleaning-up, spilled substances.
- Describe the process for collection, handling, storage, and disposal of spill wastes anticipated for various spill scenarios, including a loss of containment scenario.
- Describe the process and procedures to report and monitor all spills and spill response progress.
- Provide the decision criteria and flow chart to be used for determining the appropriate spill countermeasures.
- Describe the criteria and procedures to monitor the effectiveness of each response strategy and method.
- Provide an inventory of dedicated and readily-deployable spill-response equipment, materials, and communications equipment and facilities, and identify expected mobilization and field deployment response times.
- Describe the training qualification requirements and competency measures for personnel.
- Describe the scope and frequency of any pre-drilling and operational spill-response exercises intended to test response and further verify effectiveness of response strategies, methods, and emerging technologies.
- Describe how emergency response procedures will provide for appropriate coordination with relevant municipal, territorial, and federal emergency response plans and mutual aid agreements. Include the sharing or augmenting of response resources.
- Identify any responder roles and response equipment and training that may be provided to community-based responders.
- Describe the plan to monitor adverse impacts to the natural environment from significant or persistent spills.
- Describe the procedures for identifying clean-up priorities for potentially impacted valued environmental, physical, and socio-economic components.
- Describe the criteria and procedures for both short-term and long-term monitoring and reporting of the impact of spill countermeasures on the natural environment.
4.0 Well Approval
An operator who has obtained an Operations Authorization and who intends to drill, re-enter, workover, complete, recomplete, suspend, or abandon a well or part of a well shall obtain a Well Approval in accordance with section 10 of the COGDPR.
4.1 Well Description
Goal
The application includes essential information about the drilling program and geological conditions to ensure safety and integrity of the drilling operation.
Filing Requirements
- Provide a description of the well, including:
- the purpose of the proposed well and an overview of the drilling program;
- schematics of the proposed well illustrating the hole sizes, casing and cementing program, and other information necessary to illustrate the proposed well design;
- identification and description of the target formations, emphasizing structural and depositional interpretations, and rationale for selecting the well location and target formations;
- the directional plan;
- the formation temperature, formation pressure and fracture gradients;
- the plans for conducting leak-off tests or formation integrity tests; and
- the well data acquisition plan.
- 2. Describe how environmental factors during winter operations, including extreme temperatures, limited daylight, and remoteness of the operations could potentially affect the work or activity.
4.2 Detailed Drilling Schedule
Goal
The application describes the operations plan in enough detail to demonstrate how well operations, including critical operations, will be completed within a safe operating season.
Filing Requirements
- Provide a detailed schedule showing each drilling and completions operations.
- Provide approximate durations of critical operations that include hydraulic fracturing and formation flow testing.
- Indicate how a relief well described in the Contingency Plan is incorporated in the drilling program.
4.3 Geophysical Assessment
4.3.1 Geophysical Hazards Identification
Goal
The application describes the geophysical potential hazards in enough detail to demonstrate that the applicant has taken all reasonable precautions and used industry best practices to identify and manage hazards.
Filing Requirements
- Identify geophysical drilling hazards including, but not limited to, permafrost, active faulting, natural seismicity, shallow gas, and karst.
- Describe the mitigative and preventive measures that would be used to manage the risks during drilling and hydraulic fracturing.
4.3.2 Identification of Target Formations, Faults and Seismic Attributes
Goal
The application describes the oil and gas target formations in sufficient detail to demonstrate that the best available technology and industry best practices have been considered.
Filing Requirements
- Provide an interpretation of all faults, especially delineating major faults that may connect the target formations to the groundwater zones.
- Provide isopach and structure maps of the target formations.
- Explain how seismic attributes have been used for structure and reservoir quality identification (e.g. coherence).
4.3.3 Geophysical Data for Hydraulic Fracturing
Goal
The application describes how geophysical data has been considered and incorporated into the hydraulic fracturing program design in accordance with industry best practices.
Filing Requirements
- Identify the data needed to model the fracturing geometry and complexity and describe how it was or will be acquired.
- Identify the tools and methods that will be used to monitor the fracture propagation, including but not limited to, microseismic, tiltmeter or fluid tracer.
- Outline the means by which the petrophysical, geochemical and geomechanical properties of the target, overlying and underlying formations have been or would be acquired.
- Demonstrate how the petrophysical, geochemical and geomechanical properties of the target, and the overlying and underlying formations would be used to determine whether fracture propagation is enhanced, prevented or inhibited.
- Using the empirical data obtained from the subject wells and/or adjacent wells, submit the geomechanical properties of the overlying and underlying formations to demonstrate there are effective fracture barriers.
- Indicate how updates to the analysis and interpretation of fracture geometry and propagation would be incorporated during the hydraulic fracturing operations.
- Describe the process of evaluation of the predicted and actual fracture geometry, especially as it relates to fractures that extend beyond the target formations.
- Describe how the geophysical data was used and/or will be used to assist in hydraulic fracturing operations, such as:
- seismic volume with interpretation of faults, groundwater zones, target formation and wellbore trajectory; and
- time depth curves and velocity profile.
4.3.4 Monitoring and Reporting of Suspected Seismic Events
Goal
The application describes with sufficient detail:
- how a suspected seismic event may be monitored during drilling, completions, hydraulic fracturing and formation flow testing operations; and
- a safety termination plan, should a suspected seismic event result in a safety shutdown or disruption to drilling, completions, hydraulic fracturing or formation flow testing operations.
Filing Requirements
- Provide a reporting plan if a suspected seismic event occurs.
- Describe how oil and gas drilling, completions, hydraulic fracturing and formation flow testing operations will be safely terminated if a suspected seismic event occurs during operations.
4.4 Drilling Program
4.4.1 Groundwater Protection
Goal
The applicant’s drilling program demonstrates that effective measures are in place to protect groundwater zones from the impacts of drilling and hydraulic fracturing operations.
Filing Requirements
- Describe the policies and procedures of the drilling and hydraulic fracturing program that address groundwater protection.
- Describe the process to identify groundwater zones that includes use of technology such as sample analysis, drilling log, cased hole log and open hole logs.
- Identify possible groundwater contamination pathways from drilling and hydraulic fracturing operations, and measures to prevent this contamination.
For additional filing requirements regarding surface and groundwater protection, see Section 3.8 Safety Plan, and Section 3.10 Environmental Protection Plan.
4.4.2 Well Casing and Cementing
Goal
The application must demonstrate that the proposed well casing and cementing will isolate and protect groundwater and permafrost from drilling and hydraulic fracturing operations.
Filing Requirements
- The applicant demonstrates that:
- the surface casing is designed to isolate groundwater zones and permafrost from potential oil, gas and/or saline water zones, and the casing program provides wellbore integrity particularly in the casing annuli;
- the surface casing is designed to be set below all known or reasonably estimated utilizable groundwater zones and permafrost;
- the cement slurry design and cementing program are designed to prevent any movement of formation fluids and/or fracturing fluids in the casing annuli;
- conductor pipe and surface casing cementing programs are designed to ensure casings are cemented to surface; and
- the intermediate casing or the next set of casing after the surface casing would be cemented to surface.
- Describe how cement bond logs will be used to evaluate well control barriers to address the anticipated formation pressure and hydraulic fracturing pressure.
- Identify potential loss circulation zones, loose formations and any other factors that may affect the casing and cementing program. Demonstrate how all these factors are considered in the casing and cementing design and execution plan.
- Describe the casing pressure testing process and the criteria for a successful pressure test. Describe how the casing will be pressure tested to maximum anticipated formation pressure and to pressure, so that wellbore integrity is ensured.
- Describe the quality control and testing procedures for the casing and casing accessories, including the shoe track and casing float system that will withstand maximum hydraulic fracturing pressure.
4.4.3 Drilling Fluids
Goal
The application describes the drilling fluids system and program with sufficient detail, such that the following are demonstrated:
- well control is maintained at all times;
- the system and associated monitoring equipment is designed, installed, operated, and maintained to provide an effective barrier against formation pressure; and
- the system and associated monitoring equipment is designed, installed, operated, and maintained to allow proper well evaluation while drilling safely without polluting the environment.
Filing Requirements
- Demonstrate that the drilling fluids program addresses industry best practices for drilling fluids safety, quality control, handling and storage.
- Describe the drilling fluids testing and monitoring program to accurately measure flow rate, volumes, density, and other properties.
- Identify the minimum inventory of drilling fluids and material to maintain well control according to industry best practices.
- Describe the indicators and alarms associated with the drilling fluids system, which should be capable of accurately measuring, displaying, and recording all parameters that may indicate a hazard to personnel, affect the integrity of the well and loss of well control, or indicate a possible loss of drilling fluids in the formation.
4.4.4 Wellbore Integrity (wellbore, annulus, inter-wellbore)
Goal
The applicant provides enough detail to demonstrate that:
- at least two independent and tested physical well barriers are in place during each phase of well operations;
- well barriers ensure well integrity at all times during the well life cycle, and under all load conditions including completion and hydraulic fracturing operations; and
- if the well control is lost or if safety, environmental protection or the conservation of resources is threatened, the applicant will take any action necessary to rectify the situation without delay, despite any condition to the contrary in the well approval.
Filing Requirements
- Identify and describe the well barriers for each phase of drilling and completions operations that includes perforation, hydraulic fracturing and formation flow testing.
- Demonstrate sufficient well barriers would be in place inside the tubing and casing annuli to prevent contamination of groundwater and the environment from the reservoir and/or wellbore fluids.
- Describe the testing method and procedure for well barriers and demonstrate that each of the physical well barriers qualify as an independently tested barrier and is monitored and maintained during and after the hydraulic fracturing operations.
- Identify and describe the well barrier policies, procedures and work instructions that ensure that personnel are aware of the well barrier envelopes at any given point in time.
- Identify and describe the monitoring program in place to ensure that well integrity is maintained throughout the life of the well.
4.4.5 Well Control System
Goal
The application describes the well control system with enough detail to demonstrate that during all well operations, reliable well control equipment is installed to control flows and/or loss, prevent blow-outs, and safely carry out all well activities.
Filing Requirements
- Identify the minimum blow-out preventor (BOP) requirement for the proposed activities, and demonstrate how the proposed BOP is appropriate, adequate, and effective for the proposed well.
- Describe the well control system to be used and how the equipment meets the best industry standards and practices.
- Describe the processes to be used for equipment selection, testing, and maintenance that are critical to safety which will ensure well control in all foreseeable conditions and circumstances
- Describe how the proposed well control systems are adequate for well operations including drilling, open-hole and cased logging, perforation, hydraulic fracturing and formation flow testing.
- Provide evidence that the BOP stack is designed for the specific drilling operation and appropriate for the proposed well, and that the BOP stack:
- has not been compromised or damaged;
- will operate in the conditions in which it will be used; and
- has been maintained according to the original manufacturer’s specifications.
- Describe the process to ensure that no unauthorized modifications are made to any of the equipment that is critical to safety.
4.4.6 Relief Well Capability
Goal
The application demonstrates the capability to drill a relief well within the same drilling season to kill an out of control well.
A relief well is one contingency measure employed to respond to loss of well control. If there is a loss of well control, an operator is expected to use all available means to bring into control a well blow-out while designing, mobilizing, and undertaking a relief well operation.
Filing Requirements
- Describe the plans and procedures to kill an out-of-control well.
- Identify the drilling unit that will be used and provide a mobilization plan.
- Provide an estimate of the time that it would take to drill the relief well and kill the out of control well.
4.5 Well Completion and Hydraulic Fracturing Operations
4.5.1 Well Completion Operation
Goal
The application describes the well completion program including the unconventional resources hydraulic fracturing operations with enough detail to demonstrate that the testing of any completion interval is conducted safely and does not cause waste or pollution and that all barriers are tested to the maximum pressure to which they are likely to be subjected.
Filing Requirements
- Demonstrate that the well control system and operations will be designed, utilized, maintained, and tested as necessary to control the well in each phase of completion operations.
- Demonstrate how the well will be continuously monitored during well completion operations, particularly monitoring pressure in the casing annuli during the hydraulic fracturing operations.
- Demonstrate that the operating system meets or will exceed the requirements to which they may be subjected and will follow industry best practices.
- Describe how wellhead equipment is designed to operate safely and efficiently under the maximum load conditions.
4.5.2 Hydraulic Fracturing Design
Goal
The application demonstrates:
- how the applicant has considered all the possible hydraulic fracturing design variables for the targeted formations, and at minimum follows the industry best practices; and
- how the hydraulic fracturing will be conducted safely while protecting the environment.
Filing Requirements
- Describe the policies, procedures, and methods for modeling the hydraulic fracturing program.
- Identify the design variables that are critical to fracture propagation including:
- in-situ stresses and the choice of the creation of transversal and longitudinal fracture;
- selection of fracture treatment;
- perforations and orientation of the well;
- spacing of the fracture and fracture length, height, and width;
- optimization proppant laden fluid volume;
- control of proppant flowback; and
- method to evaluate each fracture.
- Describe the policies and procedures to maintain threshold pressure limit during hydraulic fracturing operations and how personnel will be informed of the pressures, rates and densities at any given point in time during the hydraulic fracturing operation.
- Describe the design basis for the selection of the fracturing fluids and chemical additives for the proposed hydraulic fracturing program.
- Demonstrate that the wellbore integrity is considered in the hydraulic fracturing design.
- Describe how the proposed hydraulic fracturing program addresses any risks for inter-wellbore communication of the nearby wells.
- Describe how owners of affected suspended and abandoned offset wells would be notified of a proposed hydraulic fracturing operation.
4.5.3 Hydraulic Fracture Operations
Goal
The applicant describes the well hydraulic fracturing equipment and operation with enough detail to demonstrate that the safety of the workers is maintained and that hydraulic fracturing will not cause waste or pollution. The applicant must also demonstrate that all equipment is tested to the maximum pressure to which it is likely to be subjected.
Filing Requirements
- Describe the policies and procedures to monitor wellbore annuli during hydraulic fracturing operations.
- Describe in detail how the equipment, procedures and resources are adequate to support and complete proposed hydraulic fracturing and formation flow testing operations.
- Describe the policies and procedures for testing surface and downhole equipment before commencing hydraulic fracturing operations.
- Describe in detail the on-site storage capability for produced fluids including flowback fluids and formation fluids.
- Describe in detail the handling, treatment, disposal and waste management capabilities for the fracture fluids, flowback fluids and other used or un-used chemicals.
- Describe the applicant’s policies and processes to monitor suspended and abandoned offset wells during hydraulic fracturing of the well.
4.5.4 Formation Flow Tests
Goal
The application describes the formation flow testing program based on industry best practices with enough detail to demonstrate that:
- formation flow testing will be conducted when well conditions and weather permit, without endangering personnel and equipment and harming the environment;
- formation flow testing will evaluate the productive capacity or injectivity potential of the formation;
- formation flow testing will establish reservoir and rock characteristics and properties;
- all produced fluids including flowback fluids and formation fluids will be adequately measured and recorded, sampled and analyzed;
- flaring is minimized; and
- formation flow testing will not adversely affect the ultimate recovery of oil and gas from the target formation.
Filing Requirements
- Provide the objectives of the formation flow test program including the type of information that is expected to be derived from the test.
- Provide the formation flow test procedures including the precautions that will be taken prior to, during and at termination so that the tests would be conducted and terminated in a safe, controlled, and environmentally responsible manner in accordance with Section 34 of the COGDPR and industry best practices.
- Provide the following for the formation flow test program:
- a description of any load and/or injection fluids that are to be used during the tests and estimates of the volumes;
- a description of the formations to be tested including depths, estimated pressures, estimated temperatures, and anticipated reservoir fluids;
- a list of all planned flow/injection and build-up/fall-off periods with durations and the rationale for selecting those durations;
- estimates of the flow rates or injection rates;
- a description of anticipated formation fluids;
- a description of how all produced fluids, including flowback fluids and formation fluids, would be measured and recorded;
- a description of the produced fluid sampling and analysis program, including frequency;
- a description of disposal options considered;
- a description of how and where the produced fluids including flowback fluids and formation fluids would be separated, temporarily stored, transported and disposed;
- a description of how the formation flow test will be conducted and terminated in a safe, controlled and environmentally responsible manner in accordance with best industry practices; and,
- a description of how the formation flow test is designed to acquire data necessary to assess productive capacity or injectivity potential of the target formation in accordance with best industry practices.
4.5.5 Well Suspension and Abandonment
Goal
The application describes the well suspension and abandonment program with enough detail to demonstrate that the suspended or abandoned well satisfies the requirements of the COGDPR and meets or exceeds industry best practices.
Filing Requirements
- Describe plans, policies and procedures, materials, and equipment needed to facilitate the orderly suspension of operations and securing of the well.
- Demonstrate how the suspended or abandoned well can be readily located.
- Describe how the well will be suspended or abandoned with downhole and wellhead schematics. Demonstrate that at least two tested well control barriers are in place.
- Described how the well would be tested for surface casing vent flows and if surface casing vent flows exist, describe the surface casing vent flow would be addressed in the well suspension and abandonment program.
- Identify and describe in detail the effective well barriers that are in place for the suspended or abandoned wells to prevent groundwater contamination from the reservoir fluids and/or wellbore fluids. Demonstrate that the well barriers remain effective after the hydraulic fracturing operations.
- Provide the estimated duration of suspended status of any well proposed to be suspended, and describe future plans for the well.
- Describe in detail the policies, procedures and monitoring program for planned temporary well suspension during completion and well testing operations.
- Describe how the suspended well will be monitored and inspected, to ensure its continued integrity and to prevent pollution as applicable.
5.0 All-Season Well Pads
Goal
The application describes plans for proposed all season well pads with enough detail to demonstrate that, when an all-season well pad is proposed, it will be constructed, maintained and decommissioned in a manner that will be safe and will protect the environment.
Filing Requirements
- Provide a description of the proposed design of any all-season well pad(s) including:
- the dimensions of the all-season well pads;
- the maximum number of wells that the all-season well pads may accommodate;
- how the design of the all-season well pads would safely accommodate oil and gas operations including concurrent operations and emergency egress;
- how the design of the all-season well pads would minimize impacts to the environment including wetlands and permafrost; and,
- the rationale for the set-back distances of the all-season well pad from any surface features and/or infrastructure.
- Provide a description of the safety precautions and any mitigative measures for environmental impacts that would be undertaken during the construction of the all-season well pad.
- Provide a timeline for the construction of the all-season well pad.
- Provide a description of the all-season well pad maintenance program including, if applicable, a permafrost integrity monitoring and management plan.
- Provide a general description of decommissioning and reclamation plans for the all-season well pad.
6.0 Inter-Well Distances on Multi-Well Pads
Goal
The application sufficiently demonstrates that the proposed inter-well distances will allow for safe operations, protect the environment and optimize the recovery of hydrocarbons.
Filing Requirements
Subsurface Inter-Well Distances on Multi-Well Pads
- Provide the rationale for the proposed subsurface inter-well distances of wells located on multi-well pads as it relates to the optimizing the fracture network and the optimal recovery of hydrocarbons.
Surface Inter-Well Distances on Multi-Well Pads
- Provide the rationale for the proposed surface inter-well distances of wells located on multi-well pads.
- If concurrent operations are proposed, provide a concurrent operations plan that describes how the risk of collisions, fire and worker safety would be managed during concurrent operations including information on the following:
- the chain of command, communication and coordination;
- the preventive and mitigative measures that would be utilized for collision avoidance, fire safety, worker safety and the protection of existing wellheads and facilities; and
- emergency coordination and fire control.
- Provide a permafrost integrity monitoring and management plans, for locations where permafrost exists, including information on the following:
- a description of how the proposed inter-well distance would affect the integrity of the permafrost during operations including production operations;
- the mitigative measures that would be utilized to protect the permafrost; and
- a description of how the integrity of the permafrost would be monitored.
Please refer to the Board’s Draft Spacing Order for the requirements relating to the protection of the correlative rights of adjacent licences and joint production arrangements.
- Date modified: